Welding SUpplies Online
Every welding application is different, but you can rest assured that our site will empower you with the knowledge and products you need to improve business operations. Plus, proper welding eliminates the expense of total repairs—learn more about our welding supplies online.
Who We Are
Muggy Weld provides high-quality alloys and electrodes for welding aluminum, pot metal, cast iron, steel, and various other metals. Our rod and flux combinations boast high-quality composition and work synergistically, making them perfect for organizations who want to save time and money on repairs.
Unique Product Benefits
There are several welding products on the market, but ours possess unique benefits. For instance, our electrodes for cast iron welding have a softer, highly machinable metallurgical makeup, allowing for added weld elongation. Additionally, our Super Alloy 1 pot metal restoration kit has a cooler melting point than many other rods, making pot metal application easier. We pride ourselves on providing top products that eliminate downtime and costs—you can always count on Muggy Weld.
Flip Through Our Videos
Having a visual aid is always helpful. We have provided an assortment of videos for you to learn about or brush up on welding techniques. Simply choose the topic you are interested in, and we will provide you with everything you need to know. It is one thing for a welding company to provide products—Muggy Weld likes to go above and beyond by offering educational resources.
Welding is not an easy process, but the right information can help you master MIG, TIG, arc, or other techniques. Whether you are performing cast aluminum repair, cast iron repair, stainless steel welding, or welding for just about anything else, our solutions will make life easier.
Check out The Muggy Weld Knowledge Center to learn more about our online welding supplies.
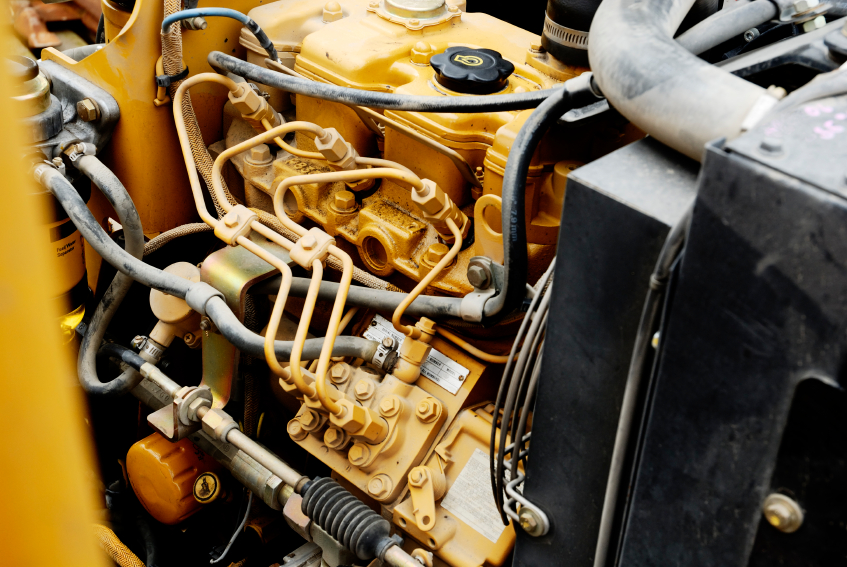
Cast Iron
Cast iron is a ubiquitous metal, used in industrial products of all types due to its versatility. It’s often chosen for its strength and affordability, but it can also provide problems for welders. However, anyone in the industry needs to be prepared to deal with cast iron, as it’s a material that they are likely to find themselves working with. Cast iron may seem like it presents several difficulties, due to its temperamentality and its delicate makeup, but with the right tools and materials, welding with cast iron is easier than you might think.
Many welders find it difficult to work with cast iron because they don’t have the appropriate materials. Nickel rods are usually harder than the base metal, making it more likely that the base metal will crack. However, our cast iron electrodes are designed to be softer and provide a greater elongation, up to 300 percent more than other roads. This reduces the chance of the base metal and weld cracking, and there’s no need for preheating or special cooling.
Cast Iron Welding
Our cast iron welding videos have been created to empower you with the knowledge that you need to successfully weld cast iron. Cast iron welding can be difficult, so we have a range of resources that will help you to understand all of the essential things you should be doing to get it right. We don’t just want to sell our products to you and abandon you to figure out what to do with them. We’re passionate about educating welders on how to use our products and improve their skills.
Use our cast iron welding videos to learn how to weld everything from a John Deere 1010 Loader to cast iron engine blocks. We have videos to help you with each of our cast iron welding products.
SSF-6 Silver Solder – This cadmium-free silver solder can braze cast iron exhaust manifolds and is a great choice for repairing HVAC systems to copper plumbing.
72 Electrode – A nickel-free cast iron welding rod designed to bond burnt or heat affected cast iron.
75 Electrode – A nickel iron non-conductive cast iron welding rod specially formulated to weld ductile, nodular, and malleable cast irons.
77 Electrode – Our premium cast iron welding rod produces machinable welds that are high-strength, resistant to cracking and porosity-free.
Take a look at our videos on the cast iron welding process to learn about how to use our products and different welding applications involving cast iron.
77 Non-Cracking Cast Iron Welding Rod | 72 Burnt Cast Iron Welding Rod | 75 Nickel Iron Rod for Malleable Ductile and Nodular Cast Iron | SSF-6 High Strength 56% Silver Solder | |
---|---|---|---|---|
Sizes Available (in.) | 5/32in, 1/8in, 3/32in | 5/32in, 1/8in, 3/32in | 3/32in, 1/8in, 5/32in | 1/16in |
Sizes Available (mm) | 3.96mm, 3.17mm, 2.38mm | 3.96mm, 3.17mm, 2.38mm | 2.38mm, 3.17mm, 3.96mm | 1.58mm |
Arc – TIG – Braze | Arc – TIG | Arc – TIG | Arc – TIG | Braze |
Works on engine blocks? | Yes | No | No | Yes |
Works on large cast iron holes? | Yes | Yes | Yes | No |
Joins cast iron to steel? | Yes | Yes | Yes | No |
Joins cast iron to metals other than steel? | No | No | No | Yes |
Works on exhaust manifolds, woodstoves, or other burnt cast iron? | Good | Great | No | Good |
Works on thin cast iron? | Yes | Yes | Yes | Yes, even very thin |
Color match? | Good | Good | Good | No |
All position? | Yes | Yes | Yes | Yes |
Machineable? | Yes | No | Yes | Yes |
Paintable? | Yes | Yes | Yes | Yes |
Works over existing welds? | Fair– better on unwelded surface | Fair | Over nickel, yes | Great |
Crack resistant? | Yes | No | No | Yes |
Depth to bevel cracks | 3/4 through | 3/4 through | 3/4 through | 1/2 through |
Cast Iron Welding Videos
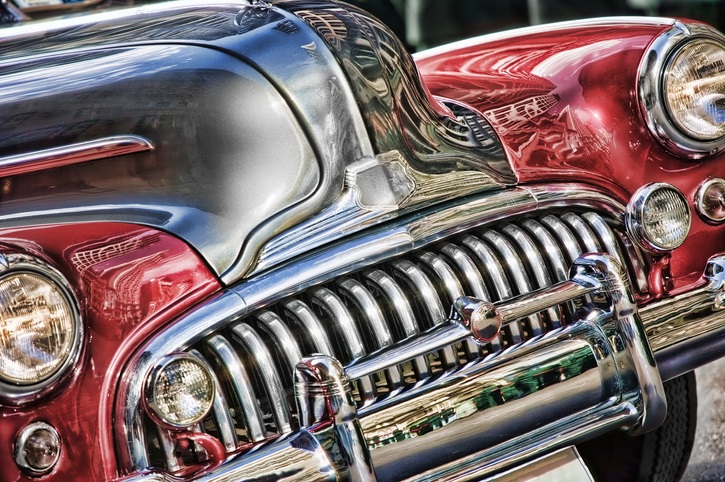
Pot Metal
Pot metal is a soft, low-quality, ferrous metal alloy comprised of zinc, copper, aluminum, tin, iron, lead, cadmium, and magnesium in varying quantities. With a low melting point of 786°F, pot metal can be difficult to restore or repair without the proper tools. Very few solders have a low enough working temperature to ensure safe repair of pot metal–many rods melt at 700º F and can be dangerously close to melting the pot metal before you even apply them.
Fortunately, Super Alloy 1 pot metal restoration kit from Muggy Weld has a melting point of 350ºF and unique properties that make pot metal welding and repairs easier than ever before. Whether you’re soldering pot metal for a repair job, repairing a priceless heirloom, or restoring original pot metal classic car parts, you can restore pot metal with ease and prevent it from pitting or breaking easily when you use quality pot metal restoration rods from Muggy Weld.
Super Alloy 1 Pot Metal Repair Kit includes both the alloy rods and a jar of liquid flux. To help prevent overheating the base metal, the non-corrosive flux acts as a temperature guide and turns root beer brown when the base metal reaches 350º F. The alloy rod and flux work synergystically, helping anyone make repairs that are as strong the base metal.
Pot Metal Repair
Muggy Weld’s pot metal repair videos have been created to empower you with the knowledge that you need to successfully restore your own pot metal parts. From antique auto and classic car parts, to Matchbox cars, antique jewelry, statues and lamps, our pot metal repair videos are a wealth of tips and techniques for successful pot metal repairs–with your own torch, in minutes.
Take a look at our videos on the pot metal restoration process to learn about how to use our products and different repair applications involving pot metal, white metal, monkey metal, zinc die cast, spelter, pewter, or lead.
Super Alloy 1 Multi-Metal and Pot Metal Solder | |
---|---|
Sizes Available (in.) | 3/32in, 1/8in |
Sizes Available (mm) | 2.38mm, 3.17mm |
Melting temperature | 350° F (177° C) |
Bonding strength | 20,000 PSI |
Flux type and shelf life | Honey liquid, 2 year shelf life |
Recommended torch | Propane, MAPP, butane, oxyacetylene |
Contains cadmium? | Yes |
Alloy color | Silver |
Metal warpage? | No |
Can bond thick to thin metals? | Good |
Can join copper, brass, and bronze to other metals? | Yes |
All position? | Yes |
Can be plated? | Most metals except aluminum |
Can be polished? | Yes |
Takes powder coating? | Yes |
Pre-cleaning necessary? | Yes, with a wire brush, sanding, Dremel etc |
Pot Metal Welding Videos
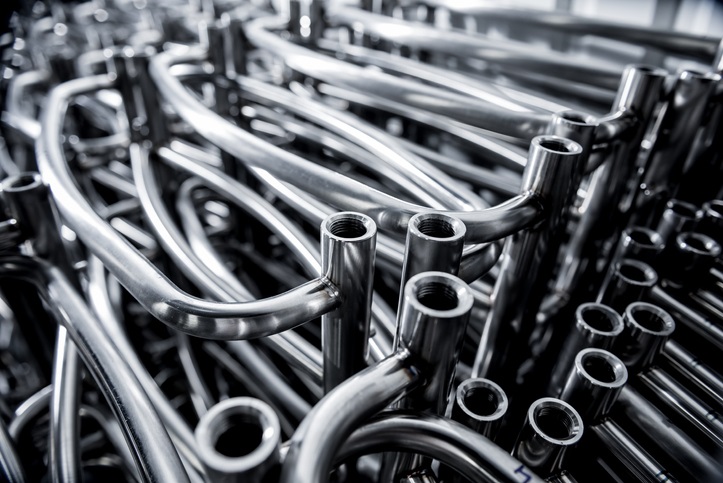
Aluminum
These days, more and more parts are being replaced with aluminum parts. Why? Aluminum is lightweight, durable, and inexpensive in comparison with other metals. The problem is, most aluminum welding shops have been trained to believe that expensive machinery is needed to properly weld this versatile metal, leaving consumers in need of an easy way to weld aluminum.
Aluminum melts at 1218°F and does not turn red like other metals before it reaches the point that it liquefies. If you have ever tried to weld aluminum you know that without an accurate temperature guide, you may end up cleaning aluminum off the floor. For this reason, many auto body shops previously recommended replacing aluminum parts rather than repairing them—which is not only expensive but unnecessary. Fortunately, times have changed, and there’s now a simple way to weld aluminum.
Muggy Weld’s aluminum welding, brazing, and soldering store contains a unique line of aluminum welding, brazing and soldering alloys and fluxes that work together to act as an exact temperature guide when torch welding aluminum. While many aluminum brazing products are sold without flux, we believe the use of flux to be superior for several reasons.
- First, it allows the rod to flow and bond better than aluminum rod alone. Any welder knows that flow is an important factor in a successful aluminum soldering procedure. “Where flux flows, rod goes”
- Second, Muggy Weld fluxes act as exact temperature guides, changing form when the base metal reaches the proper working temperature.
- Finally, Super Alloy 5’s flux chemically reacts to clean up oxidation as well as other contaminants, which is very unique in aluminum repair procedure.
Aluminum Welding, Brazing, and Soldering
Take some time to view our aluminum welding, brazing, and soldering videos and familiarize yourself with our high quality aluminum welding repair products:
Super Alloy 1 is a low temperature solder that bonds aluminum at 350ºF. Super Alloy 1’s special formulation bonds aluminum to a number of other metals including brass, steel, and pot metal
Super Alloy 5 is our high strength brazing alloy specifically designed for aluminum repair. Super Alloy 5 can be used as TIG rod, or can be applied with nearly any brazing torch to weld aluminum at only 600ºF
Even if you’ve never held a torch, our aluminum welding videos will empower anyone to successfully repair aluminum parts. From aluminum boat repair to cast aluminum to delicate ac lines, our aluminum brazing and soldering products demystify aluminum welding and make it approachable to welders of all skill levels.
Super Alloy 1 Multi-Metal and Pot Metal Solder | Super Alloy 5 Aluminum Welding and Brazing Rod | |
---|---|---|
Sizes Available (in.) | 3/32in, 1/8in | 3/32in, 1/16in |
Sizes Available (mm) | 2.38mm, 3.17mm | 2.38mm, 1.58mm |
Melting Point | 350° F (177° C) | 600° F (316° C) |
Bonding Strength | 20,000 PSI | 30,000 PSI |
Flux type and shelf life | Honey liquid, 2 year shelf life | Powder, 1 year shelf life |
Recommended torch | Propane, MAPP, butane, oxyacetylene on larger or thicker pieces | Propane, MAPP, oxyacetylene on larger or thicker pieces |
Can be polished? | Fair | Excellent |
Can be plated? | Yes | Yes |
Takes powder coating? | Fair | Excellent |
Can be used on thick aluminum? | No | Yes, with oxyacetylene |
Can join aluminum to other metals (brass, steel etc)? | Yes | No |
Can repair radiators without burning fins? | Yes | No |
Potential for metal warpage? | No | Potential |
Can be used with TIG? | No | Yes |
Can repair cast aluminum? | No | Yes, with oxyacetylene |
Pre-cleaning necessary? | Yes | Yes |
Can repair aluminum boats? | No | Yes, with oxyacetylene |
Can be anodized? | No | Yes |
Can be used with a soldering iron? | Yes | No |
Demonstrated on pop cans at the county fair? | NEVER | NEVER |
Aluminum Welding Videos
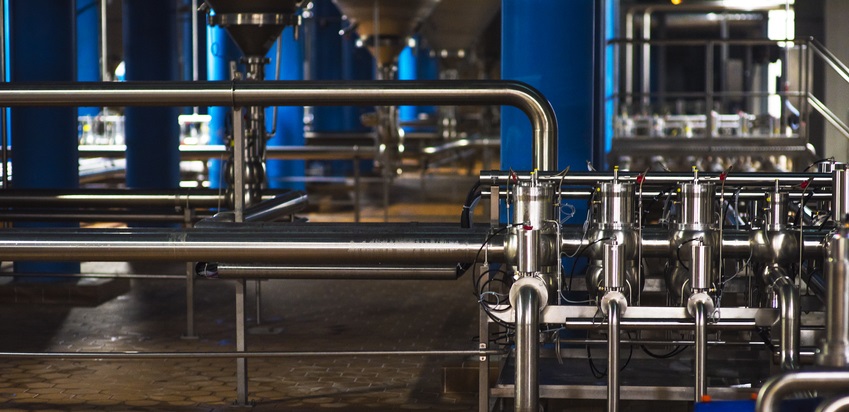
Stainless Steel
Stainless steel is an alloy containing at least 10.5% chromium and less than 1.2% carbon and other metals. Considered “green” due to its infinite recyclability and sustainability, stainless is also corrosion resistant, durable, easy to clean and maintain, and aesthetically appealing. For these reasons, stainless steel is utilized extensively in hospital, restaurant, construction, transportation, and energy production applications.
Although stainless steel is one of the most widely used metals, stainless steel welding can be extremely challenging. Cutting, drilling, soldering, and welding stainless steel is difficult mainly because the metal is a poor heat conductor and has a high rate of thermal expansion. It also reacts badly to excessive heat, causing it to warp. Thankfully, we have a unique line of products that can help make stainless steel soldering and brazing tasks easier.
Super Alloy 1, SSQ-6, and SSF-6 silver solder are all designed for brazing and soldering stainless steel. Allowing for easier and more effective repair and welding jobs, many of our products melt at high temperatures and can be used on a variety of metals, such as brass, copper, bronze, cast iron, and stainless steel. For soldering and brazing tasks, or for welding stainless steel, SSQ-6 and SSF-6 can also be used with any heat source and can last for long periods with minimal care.
Stainless Steel Welding
Super Alloy 1 is a low temperature solder that bonds stainless to a variety of other metals at 350º F
SSF-6 Silver Solder is a high strength, 56% silver solder alloy that’s both hospital and restaurant safe. SSF-6 is a perfect color match to stainless.
SSQ-6 Silver Solder Paste is a 1 oz syringe of silver solder alloy combined with high flowing flux. SSQ-6 wets stainless and burnt stainless steel, and can be used to bond stainless to many metals.
Our stainless steel welding videos were designed to simplify the stainless steel soldering and brazing process and outline our unique product line. Check out instructional stainless steel welding videos below and learn how to repair tubing, create custom pieces, join stainless to brass, steel, and and more.
Super Alloy 1 Multi-Metal and Pot Metal Solder | SSF-6 High Strength 56% Silver Solder | SSQ-6 56% Silver Solder Paste | |
---|---|---|---|
Sizes Available (in.) | 3/32in, 1/8in | 1/16in | N/A |
Sizes Available (mm) | 2.38mm, 3.17mm | 1.58mm | N/A |
Melting temperature | 350°F (177°C) | 1150°F (622°C) | 1050°F (566°C) |
Bonding strength | 20,000 PSI | Over 70,000 PSI | Over 85,000 PSI |
Flux type and shelf life | Honey liquid, 2 year shelf life | Flux coated | Mixed in, 9 month shelf life |
Recommended torch | Any | Any | Any |
Color match? | Yes | Yes | Yes |
Contains cadmium? | Yes | No | No |
Works in all positions? | Yes | Yes | Yes |
Will clean oxidized stainless? | |||
Will wet to burnt stainless? | No | Yes | No |
Will join stainless to brass, steel, copper, cast iron? | No | Yes | Yes |
Can work as a jig? | No | No | Yes |
Recommended for heat sensitive parts? | Yes | No | No |
Stainless Steel Welding Videos
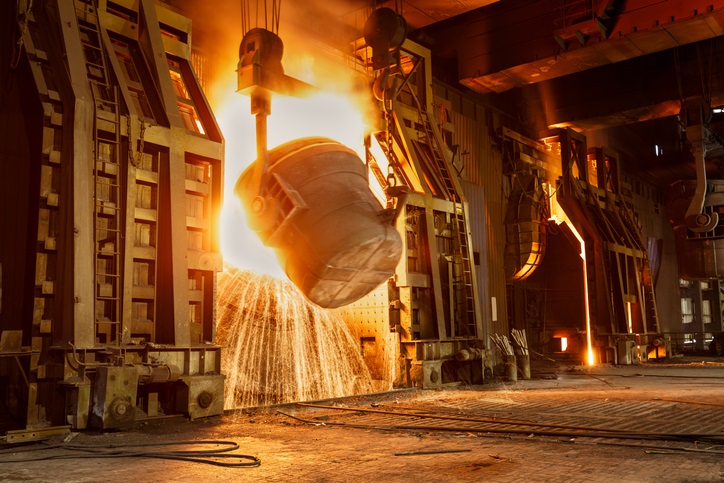
Steel
Steel is an alloy composed of iron and carbon—the higher the carbon content, the stronger, harder and more brittle the steel. There are many types of steel that can be used for steel welding jobs, all of which are categorized based upon various physical properties and carbon content.
Mild steel, also known as low carbon steel, has a carbon range of .05% to .30% Medium carbon steel has a carbon range of .30% to .45%, high carbon steel has a carbon range of .45% to .75%, and very high carbon steel has a carbon content of .75% to 1.5%. Mild steel is easily formed, machined, and welded, medium carbon steel is more brittle, and high carbon steel is very strong.
Most steel soldering or brazing jobs require only a hand held propane torch.
Super Alloy 1 is recommended when heat or aesthetics is an issue, otherwise we recommend SSF-6 Silver Solder for torch welding: with a holding strength of 71,000 PSI, SSF-6 is as strong as a MIG or TIG weld, with a beautiful finish.
Steel Welding
Steel repair can be very difficult; it is difficult to cut and is prone to distortion because of its high thermal expansion. Control the amount of ferrite in the weld to minimize hot cracking, preheat, and use steel welding and solder products such as Super Alloy 1, SSF-6, and SSQ-6 when working on different types of stainless steel.
Super Alloy 1 is a multi-metal solder that bonds steel to a variety of other metals. At 350º F, Super Alloy 1 is our lowest temperature alloy.
SSF-6 Silver Solder is a high strength, flux-coated silver solder rod. One inch of this 56% silver rod flows an amazing 18 inches and produces joints that are 70,000 psi
SSQ-6 Silver Solder Paste is presented in a convenient 1 oz syringe and contains the same solder formula as SSF-6, with the flux mixed into the paste for easy application.
Take a look at our videos below to learn about the steel brazing and soldering process and how to use our high quality products in a variety of repair applications such as: auto body, antique shotgun restoration, brake line, hydraulic line and more.
Super Alloy 1 Multi-Metal and Pot Metal Solder | SSF-6 High Strength 56% Silver Solder | SSQ-6 56% Silver Solder Paste | |
---|---|---|---|
Sizes Available (in.) | 3/32in, 1/8in | 1/16in | N/A |
Sizes Available (mm) | 2.38mm, 3.17mm | 1.58mm | N/A |
Melting temperature | 350° F (177° C) | 1150° F (621° C) | 1050° F (566° C) |
Bonding strength | 20,000 PSI | Over 70,000 PSI | Over 85,000 PSI |
Flux type and shelf life | Honey liquid, 2 year shelf life | Flux coated | Mixed in, 9 month shelf life |
Recommended torch | Propane, MAPP, butane, oxyacetylene | Any | Any |
Contains cadmium? | Yes | No | No |
Color match? | No | Good | Good |
Works in all positions? | Yes | Yes | Yes |
Works for heat sensitive parts? | Great | Fair | Fair |
Steel Welding Videos
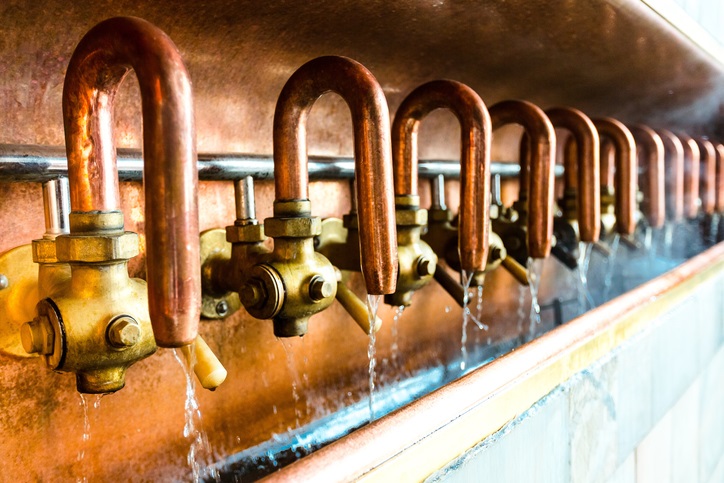
Copper, Brass, Bronze
Copper is a corrosion resistant, non-ferrous metal used extensively in construction, industrial machinery, wire and cable products, and copper tubing due to its strength, antimicrobial properties, and thermal and electrical conductivity. Pure copper has a high melting point of 1983º F; however, there are hundreds of copper alloys: copper-lead, aluminum bronze, copper silicon, copper zinc, copper nickel or cupro-nickel, and copper tin.
Here are some things to remember when brazing or soldering brass, bronze, or copper:
Brass is a copper-zinc alloy that melts at around 1652-1724º F range and is fairly easy to cast. Brass is commonly used to create musical instruments such as trumpets or trombones, as well as bathroom fixtures and doorknobs. During any brass brazing or soldering job, use high quality filler if the color doesn’t have to match the metal.
Bronze is an alloy of copper, tin, aluminum, or silicon with a melting point of 1675º F. Cold-working or heat treating bronze increases its tensile strength, making it an attractive choice for industrial applications, musical instruments, medals, art and sculpture.
Copper, Brass, and Bronze Repair
While copper, brass, and bronze may not be applications that are used every day in welding, industries such as refrigeration, electronics and plumbing—as well as ornamental artists, encounter these metals and perform brass, bronze, or copper welding jobs daily.
Super Alloy 1 can bond all of these metals in any combination, and can be used in bonding with other metals such as aluminum—at 350º F.
SSF-6 Silver Solder is 56% silver, cadmium-free and is especially useful when high strength is needed, or when you need high flow to get to those hard to reach areas.
SSQ-6 Silver Solder Paste is the same formula as our SSF-6, in a convenient 1 oz syringe to allow for precision application.
Copper, brass, and bronze can be easily soldered or brazed with the right tools and knowledge. Take some time to view our repair videos to learn how to use our products in different soldering and brazing applications joining copper, brass, and bronze individually and in any combination. Regardless of your welding skill level, we have videos to help you with each of our copper, brass, and bronze repair products.
Super Alloy 1 Multi-Metal and Pot Metal Solder | SSF-6 High Strength 56% Silver Solder | SSQ-6 56% Silver Solder Paste | |
---|---|---|---|
Sizes Available (in.) | 3/32in, 1/8in | 1/16in | N/A |
Sizes Available (mm) | 2.38mm, 3.17mm | 1.58mm | N/A |
Melting temperature | 350°F (177°C) | 1150°F (622°C) | 1050°F (566°C) |
Bonding strength | 20,000 PSI | over 70,000 PSI | over 85,000 PSI |
Flux type and shelf life | Honey liquid, 2 year shelf life | Flux coated | Flux mixed in, 9 month shelf life |
Recommended Torch | Any | Any | Any |
Alloy color | Silver | Silver | Silver |
Contains cadmium? | Yes | No | No |
Works in all positions? | Yes | Yes | Yes |
Potential for metal warpage? | No | Yes | Yes |
Bonds thick to thin metals? | Good | Great | Great |
Can join copper/brass/bronze to other metals? | Yes | Yes | Yes |